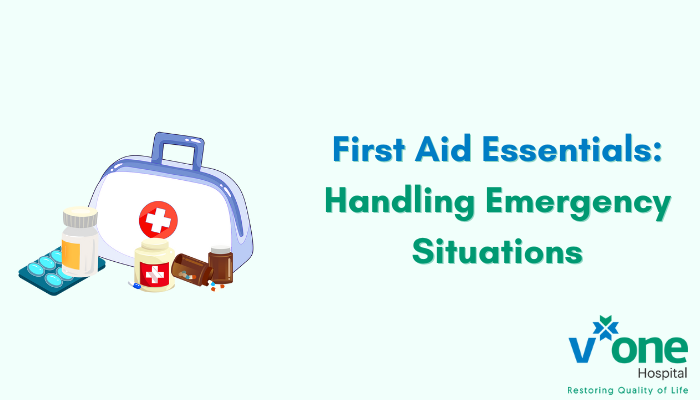
Handling Emergency Maintenance Situations Quickly and Efficiently
Emergency maintenance , those unplanned interventions that disrupt operations and demand immediate attention, are a fact of life in any industry. But how you handle these crises can make or break your organization’s productivity, profitability, and even its reputation. What if a critical piece of equipment suddenly fails, bringing your entire production line to a halt? Or imagine a facility-wide power outage that threatens sensitive data and disrupts essential services. These scenarios aren’t just theoretical; they’re real-world challenges that businesses face every day.
Emergency maintenance refers to the unscheduled repair or replacement of equipment or systems that have broken down unexpectedly. It’s the reactive approach to fixing problems that weren’t anticipated or prevented. And while some emergencies are unavoidable , many can be mitigated through proactive planning and efficient response strategies. Are you struggling to keep up with constant breakdowns and repairs ? Are you losing valuable time and resources to emergency maintenance ?
This article offers a thorough guide to handling emergency maintenance situations quickly and efficiently. We’ll explore the key strategies, tools, and optimal practices that can help you minimize downtime, reduce costs, and improve overall operational resilience. From proactive planning and risk assessment to rapid response and effective communication, we’ll cover every facet of emergency maintenance management. We will start by outlining the importance of preparation and planning, we will then dive deep into the steps for rapid response and efficient execution, and finally we will discuss the importance of post-incident examination and continuous improvement.
The Importance of Proactive Planning for Emergency Maintenance
Related Post : Dealing with the Emotional Toll of Difficult Landlord-Tenant Situations
Conducting a Thorough Risk Assessment
The foundation of effective emergency maintenance lies in proactive planning. This starts with a thorough risk assessment to determine potential vulnerabilities and prioritize potential emergency situations. A risk assessment involves evaluating your equipment, systems, and facilities to determine the likelihood and impact of potential failures. What are the critical assets that, if compromised , could cripple your operations ? What are the common causes of equipment failure in your industry ?
For example , a manufacturing plant might determine critical machinery like conveyor belts, robotic arms, and power generators as high-risk assets. A hospital might focus on life-support systems, emergency power supplies, and data servers. By understanding your specific risks, you can develop targeted prevention and response strategies. Remember the Northeast Blackout of 2003? A cascading power failure originating in Ohio plunged millions into darkness. A post-mortem examination revealed that inadequate risk assessment and a lack of coordinated emergency response plans exacerbated the impact of the initial event.
Consider using a risk assessment matrix to visually represent the likelihood and severity of potential failures. This can help you prioritize your efforts and allocate resources effectively. Regularly update your risk assessment to reflect changes in your equipment, processes, and environmental conditions. Don’t treat it as a one-time exercise; it’s an ongoing process that should be integrated into your overall maintenance plan.
Key Steps in Risk Assessment:
- determine Critical Assets: List all equipment, systems, and facilities essential to your operations.
- Determine Potential Failure Modes: Analyze how each asset could fail (e.g., mechanical breakdown, electrical failure, software glitch).
- Assess Likelihood of Failure: Estimate the probability of each failure mode occurring (e.g., low, medium, high).
- Evaluate Impact of Failure: Determine the consequences of each failure mode (e.g., downtime, financial loss, safety hazard).
- Prioritize Risks: Rank risks based on their likelihood and impact, focusing on the highest priority items.
Developing Detailed Emergency Maintenance Plans
Once you’ve identified your key risks , the next step is to develop detailed emergency maintenance plans. These plans should outline the specific procedures, resources, and responsibilities required to respond effectively to varied types of emergencies. A well-defined plan ensures that everyone knows what to do, when to do it, and how to communicate during a crisis. Who is responsible for shutting down equipment? Who is authorized to order replacement parts? Who is the point of contact for external emergency services?
Your plans should be specific, practical, and easy to understand. Avoid jargon and technical terms that might confuse personnel during a stressful situation. Include step-by-step instructions, checklists, and diagrams to guide users through the necessary procedures. Consider creating separate plans for varied types of emergencies, such as equipment failures, power outages, natural disasters, and cyberattacks. The Deepwater Horizon oil spill in 2010 highlighted the critical importance of having robust emergency response plans. The lack of clear procedures and coordination among varied parties contributed to the severity of the disaster and the prolonged recovery effort.
Regularly review and update your plans to reflect changes in your operations, personnel, and technology. Conduct drills and simulations to test the efficacy of your plans and determine areas for improvement. Involve all pertinent stakeholders in the planning process, including maintenance technicians, operations managers, safety officers, and IT specialists. Don’t keep your plans locked away in a filing cabinet; make them readily accessible to all personnel who need them.
Key Elements of an Emergency Maintenance Plan:
- Emergency Contact List: Include phone numbers, email addresses, and functions of key personnel.
- Shutdown Procedures: Detail step-by-step instructions for safely shutting down equipment and systems.
- Isolation Procedures: Specify how to isolate damaged equipment or areas to prevent further damage or injury.
- Repair Procedures: Outline the steps for repairing or replacing damaged equipment.
- Communication Protocols: Define how information will be disseminated during an emergency (e.g., phone calls, emails, text messages).
- Resource Allocation: determine the resources needed (e.g., spare parts, tools, equipment) and how to access them.
Rapid Response and Efficient Execution in Emergency Maintenance
Establishing a Clear Chain of Command
In the heat of an emergency maintenance situation, clear communication and a well-defined chain of command are essential. This ensures that decisions are made quickly and efficiently, and that everyone knows who is responsible for what. Establish a clear hierarchy of authority, with designated individuals responsible for assessing the situation, coordinating the response, and communicating with stakeholders. Who is the incident commander? Who is responsible for safety? Who is authorized to make financial decisions?
Clearly define the functions and responsibilities of each member of the emergency response team. offer them with the necessary training and authority to perform their duties effectively. Empower them to make decisions on the spot, without having to wait for approval from higher-ups. The Fukushima Daiichi nuclear disaster in 2011 underscored the importance of a clear chain of command during emergencies. Confusion and delays in decision-making hampered the initial response and contributed to the severity of the crisis.
Regularly review and update your chain of command to reflect changes in personnel and organizational structure. Communicate the chain of command to all employees and make sure they understand their functions and responsibilities. Consider using a visual chart or diagram to illustrate the chain of command. Don’t assume that everyone knows who to report to or who to contact in an emergency.
Key Elements of a Chain of Command:
- Incident Commander: The person responsible for overall coordination and decision-making during an emergency.
- Safety Officer: The person responsible for ensuring the safety of personnel and the environment.
- Operations Manager: The person responsible for managing the technical facets of the response.
- Communications Officer: The person responsible for communicating with stakeholders (e.g., employees, customers, media).
- Liaison Officer: The person responsible for coordinating with external agencies (e.g., fire department, police).
Utilizing Technology for Faster Response Times
In today’s digital age , technology can play a crucial function in accelerating emergency maintenance response times and improving efficiency. From computerized maintenance management systems (CMMS) to mobile devices and remote monitoring sensors, there are numerous tools available to help you streamline your emergency maintenance processes. Are you using technology to its full potential to improve your emergency response capabilities? Are you leveraging data analytics to determine potential problems before they escalate into emergencies?
Implement a CMMS to track equipment maintenance schedules, manage work orders, and monitor inventory levels. Use mobile devices to enable technicians to access information, report problems, and receive instructions in the field. Deploy remote monitoring sensors to detect anomalies and predict equipment failures before they occur. The use of drones for infrastructure inspection is also increasing , as they can quickly assess damage in areas that are difficult or dangerous to reach.
The integration of IoT (Internet of Things) devices can offer real-time data on equipment performance, allowing for proactive maintenance and preventing unexpected breakdowns. Data analytics can help determine patterns and trends that can predict potential failures, enabling you to take corrective action before an emergency occurs. Investing in the right technology can significantly reduce downtime, improve efficiency, and enhance overall emergency response capabilities. Consider the example of Tesla , which uses over-the-air software updates to remotely diagnose and fix problems with its vehicles, minimizing the need for emergency maintenance and reducing downtime for its customers.
Key Technologies for Emergency Maintenance:
- CMMS (Computerized Maintenance Management System): Automates maintenance scheduling, work order management, and inventory control.
- Mobile Devices: Enables technicians to access information, report problems, and receive instructions in the field.
- Remote Monitoring Sensors: Detects anomalies and predicts equipment failures before they occur.
- IoT (Internet of Things) Devices: offers real-time data on equipment performance for proactive maintenance.
- Data Analytics: Identifies patterns and trends that can predict potential failures.
Post-Incident examination and Continuous Improvement in Emergency Maintenance
Conducting Thorough Root Cause examination
After an emergency maintenance event, it’s crucial to conduct a thorough root cause examination to determine the underlying causes of the problem and prevent similar incidents from happening in the future. This involves investigating the sequence of events leading up to the failure, determineing any contributing factors, and determining the root cause of the issue. Did the failure outcome from inadequate maintenance? Was it caused by operator error? Was it due to a design flaw?
The objective of root cause examination is not to assign blame, but to understand what happened and why. Use tools like the “5 Whys” technique or the fishbone diagram (also known as the Ishikawa diagram) to systematically investigate the causes of the failure. Gather data from multiple sources, including maintenance records, operator logs, and equipment sensors. Involve all pertinent stakeholders in the examination, including maintenance technicians, operations managers, and engineers. The investigation into the Space Shuttle Challenger disaster in 1986 is a classic example of the importance of root cause examination. The investigation revealed that the disaster was caused by a failure in an O-ring seal, but also uncovered systemic problems in NASA’s safety culture and decision-making processes.
Document your findings and recommendations in a thorough report. Share the report with all pertinent stakeholders and use it to develop corrective actions. Follow up to ensure that the corrective actions are implemented and effective. Don’t let the lessons learned from the incident fade away; incorporate them into your ongoing maintenance practices.
Key Steps in Root Cause examination:
- Define the Problem: Clearly describe the failure or incident.
- Gather Data: Collect information from multiple sources (e.g., maintenance records, operator logs).
- determine Contributing Factors: Determine the factors that contributed to the failure.
- Determine the Root Cause: determine the underlying cause of the problem.
- Develop Corrective Actions: Implement measures to prevent similar incidents from happening in the future.
Implementing a Continuous Improvement Process
Emergency maintenance is not a static process; it should be continuously improved based on lessons learned and changing conditions. Implement a continuous improvement process to regularly review and refine your emergency maintenance plans, procedures, and technologies. Seek feedback from maintenance technicians, operations managers, and other stakeholders. What worked well during the last emergency? What could be improved? What new technologies or techniques should be considered?
Use data from your CMMS and other sources to track key performance indicators (KPIs) related to emergency maintenance, such as downtime, repair costs, and response times. Monitor these KPIs over time to determine trends and assess the efficacy of your improvement efforts. Benchmark your performance against industry optimal practices to determine areas where you can improve. The Toyota Production System (TPS) , with its emphasis on continuous improvement (Kaizen) , offers a valuable model for optimizing maintenance processes and reducing downtime.
Regularly update your emergency maintenance plans and procedures to reflect changes in your equipment, processes, and personnel. Conduct periodic drills and simulations to test the efficacy of your plans and determine areas for improvement. Foster a culture of continuous learning and improvement within your maintenance organization. Encourage employees to share their ideas and suggestions for improving emergency maintenance processes. Don’t be afraid to experiment with new approaches and technologies. The key to achievement is to be proactive, adaptable, and committed to continuous improvement.
Key Elements of a Continuous Improvement Process:
- Set objectives: Define specific, measurable, achievable, pertinent, and time-bound (SMART) objectives for emergency maintenance performance.
- Collect Data: Track key performance indicators (KPIs) related to emergency maintenance.
- Analyze Data: determine trends and patterns in the data to assess performance and determine areas for improvement.
- Develop Improvement Plans: Create action plans to address identified areas for improvement.
- Implement Improvements: Put the improvement plans into action.
- Evaluate outcomes: Measure the impact of the improvements on key performance indicators.
- Adjust Plans: Modify the improvement plans based on the outcomes of the evaluation.
Frequently Asked querys About Emergency Maintenance
Q1: What is the difference between preventive maintenance and emergency maintenance ?
Preventive maintenance is proactive and aims to prevent equipment failures before they occur. It involves scheduled inspections, lubrication, adjustments, and replacements to keep equipment in optimal condition. Emergency maintenance, on the other hand , is reactive and addresses unexpected equipment breakdowns that require immediate attention. While preventive maintenance reduces the likelihood of emergencies , it doesn’t eliminate them entirely. A well-rounded maintenance plan incorporates both preventive and emergency maintenance to ensure optimal equipment performance and minimal downtime. By investing in preventive measures , you can significantly reduce the frequency and severity of emergency situations.
Q2: How can I reduce the costs associated with emergency maintenance ?
Reducing emergency maintenance costs requires a multi-faceted approach. First , invest in a robust preventive maintenance program to minimize the frequency of unexpected breakdowns. Second , implement a computerized maintenance management system (CMMS) to track maintenance activities, manage inventory, and maximize resource allocation. Third , ensure that your maintenance technicians are properly trained and equipped to handle emergency situations efficiently. Fourth , negotiate favorable contracts with suppliers and vendors to secure rival pricing on spare parts and services. Finally , conduct thorough root cause analyses after each emergency to determine the underlying causes and prevent similar incidents from happening in the future. By focusing on prevention, efficiency, and continuous improvement, you can significantly reduce the financial burden of emergency maintenance.
In conclusion , handling emergency maintenance situations quickly and efficiently is not just about reacting to problems, it’s about proactive planning, clear communication, and continuous improvement. By focusing on emergency maintenance, investing in the right tools and training, and fostering a culture of preparedness, you can minimize downtime, protect your assets, and ensure the safety of your personnel. Don’t wait for the next crisis to strike; start implementing these strategies today to build a more resilient and efficient operation. Ready to take your maintenance plan to the next level ? Contact us for a consultation and discover how we can help you maximize your emergency maintenance protocols and achieve peak performance.